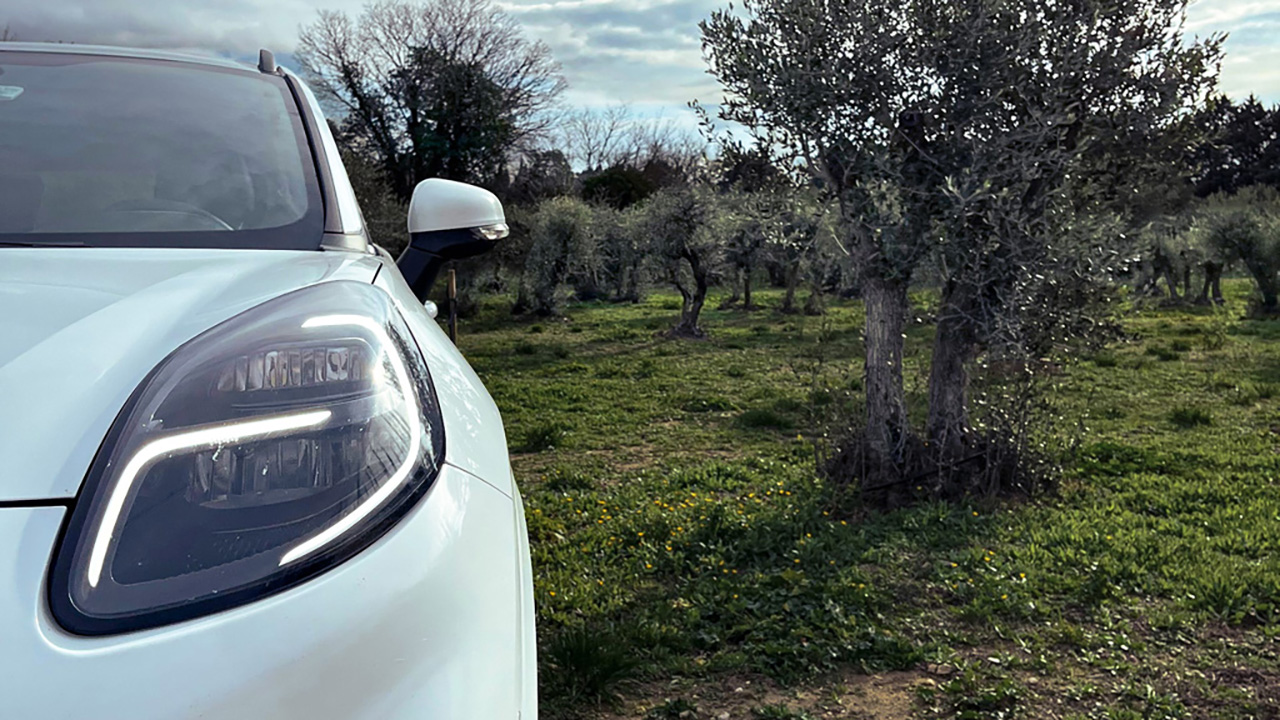
As the automotive industry grapples with the challenges of climate change and depleting resources, automakers are increasingly graduating from greenwashing to serious investment in the development of scalable, sustainably-sourced materials to integrate into their vehicles. Genesis is lining the interiors of their luxury EVs with plant-based leather, yarns extracted from sugar cane and corn are now woven into floor mats of the Hyundai IONIQ 5, and the Polestar 3’s flax-based composite parts are replacing traditional carbon fiber.
One of the more novel efforts currently in progress is being done by Ford engineers in Cologne, Germany, in cooperation with the renewable bio-composite manufacturing project, COMPOlive. The partnership gathers waste sourced from pruned olive trees in Andalusia, Spain, and converts the excess organic matter into a new category of bio-composite fiber with promising applications across the auto industry.
The injected molded parts made from 40% olive tree fibers and 60% recycled polypropylene plastic have been tested both in simulations and in real Ford vehicles to be durable enough and as a lighter weight alternative to traditional plastic, suited for use in existing interior components such as footrests.
The olive tree venture isn’t Ford’s first go around integrating sustainably-sourced materials into their fleet of vehicles. A few real world examples you can check out right now on the road today include recycled yogurt cups made into frunk inserts for the Ford Mustang Mach-E and recycled ocean plastic converted into harness clips inside the Ford Bronco Sport.
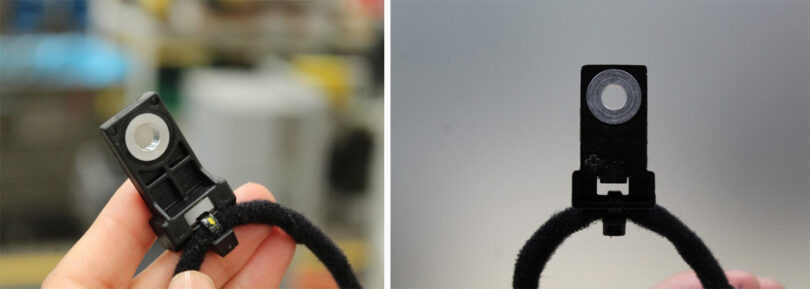
Ocean-harvested plastic – commonly referred to as “ghost gear” – is being converted into wiring harness clips in the Ford Bronco Sport.
The partnership with COMPOlive could lead to a win-win situation – Ford reduces their bottom line and their reliance on sourcing virgin plastics, while olive oil producers can turn their bio-waste into a new revenue stream. Ford currently relies upon somewhere in the ballpark of 1,400 Tier 1 production suppliers to provide vehicle parts composed of over 1,000 different materials, meaning the road toward true circular design will require a great many more innovations to meet the company’s goals of reaching carbon neutrality by 2050 globally, and by 2035 in Europe.